Unsere Kleinservoantriebssysteme dosieren Flüssigkeiten punktgenau
Die Aufgabe war anspruchsvoll: In einer Produktformungsmaschine für Spülmittelpads der Harro Höfliger GmbH sollten Flüssigkeiten mit wechselnder Viskosität exakt und prozesssicher in Pads dosiert werden – bis zu sechs Millionen Mal pro Tag. Um diese Herausforderung zu lösen, setzten die Entwickler von Harro Höfliger auf korrosionsbeständige Kleinservoantriebssysteme in Volledelstahl-Ausführung von WITTENSTEIN cyber motor. Auch deren kompakte, platz- und gewichtssparende Baugröße überzeugte auf Anhieb. Zudem bietet ein in den Antriebsverstärker integrierter Webserver ständige Konnektivität, um für Optimierungs- oder Servicearbeiten auf die Dosierstationen und jeden einzelnen Dosierantrieb zugreifen zu können.
Ein perfektes Team: Servomotoren und -aktuatoren der cyber® dynamic line
Im Portfolio der Kleinservoantriebssysteme von WITTENSTEIN cyber motor bilden die Servomotoren und Servoaktuatoren der cyber® dynamic line zusammen mit Servoreglern der cyber® simco® line kundenspezifisch konfigurierbare, hochperformante und leistungsdichte Funktionseinheiten. Unterschiedliche Leistungsbereiche der Motor-Getriebe-Einheiten, die auch in korrosions- und hygienegerechten Ausführungen verfügbar sind, sowie intelligente Servoregler mit Webserver-Funktionalität und einer Vielzahl möglicher Feldbusschnittstellen ermöglichen individuell skalierbare Antriebslösungen mit hoher Performance- und Zukunftssicherheit – wie z. B. in einer Produktformungsmaschine der Harro Höfliger Verpackungsmaschinen GmbH.
Der Produktionsprozess in aller Kürze
So ist der Ablauf: In der Vorheizstation wird eine zugeführte Folie erwärmt und per Vakuum in die Kavitäten von Produktionsplatten, die durch die Maschine getaktet werden, angesaugt. Nach einer ersten Pulverdosierung folgen die Liquidstationen, in denen jeweils 20 parallel montierte Kleinservoantriebssysteme als Dosierschneckenantriebe zum Einsatz kommen. Nachdem an der dritten Liquidstation eine weitere Komponente zugefügt wurde, wird die Oberfolie zugeführt und die Pads in der Siegelstation verschlossen. Danach wird die Pad-Matte in der Produktionsplatte in Längs- und Querrichtung geschnitten und die einzelnen Pads durch Vakuum-Greifer aus den Kavitäten entnommen.
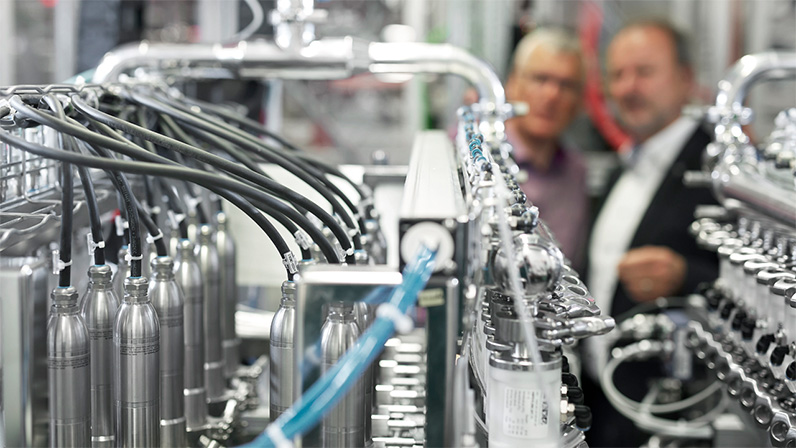