Our small servo drive systems dose liquids precisely
It was a complex challenge: liquids of varying viscosity needed to be dosed into pads efficiently and precisely in a dishwasher pad forming machine at Harro Höfliger GmbH – up to six million times a day. Harro Höfliger’s developers put their trust in small servo drive systems from WITTENSTEIN cyber motor, which are made from 100% stainless steel and hence resistant to corrosion. The compact, lightweight design likewise won the customer’s enthusiasm straight away owing to significant space saving. Moreover, the web server integrated in the servo drive provides “always on” connectivity, so that the dosing stations and each individual dosing drive can be accessed at any time for optimization or servicing.
A perfect team: Servo motors and actuators in the cyber® dynamic line
In WITTENSTEIN cyber motor’s portfolio of small servo drive systems, the servo motors and actuators in the cyber® dynamic line team up with the servo drives in the cyber® simco® line to form custom configurable, high performance and power dense functional units. The motor-gearbox units can be supplied with different output ratings and with a corrosion resistant or hygienic design; together with our intelligent servo drives offering web server functionality and numerous possible fieldbus interfaces, they enable individually scalable drive solutions that are both high performance and future proof – like the one developed for a product forming machine at packaging equipment specialist Harro Höfliger.

+49 7931 493-15800
The production process in brief
This is how it works: a film is fed to the preheating station, where it is heated and sucked by vacuum into the cavities of format sheets, which are moved through the machine in several steps. The first powder dosing station is followed by the liquid stations; 20 small servo drive systems mounted parallel to one another in each station drive the dosing augers. After adding a further component at the third liquid station, the top film is pressed on and the pads are sealed in the sealing station. The pad mat in the format sheet is then cut both lengthways and across, and the individual pads are removed from the cavities by means of vacuum grippers.
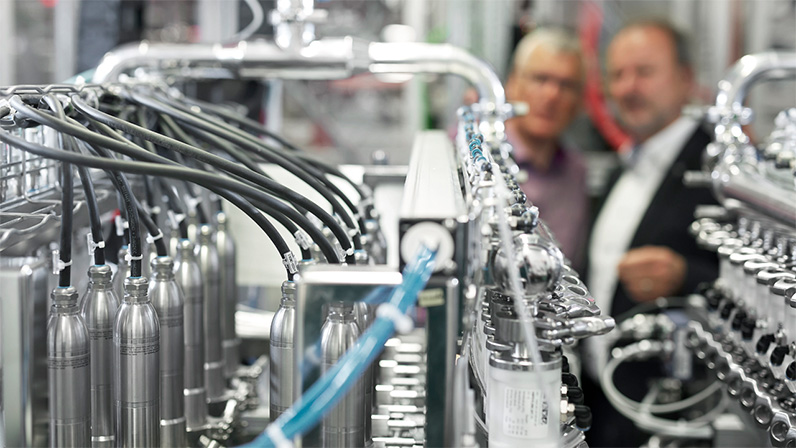