cyber® simco® drive 2 – servo drive
connective – intelligent – safe
In combination with various servo motors and servo actuators, cyber® simco® drive 2 is the ideal solution for fast and precise moving and positioning tasks. With a continuous output of up to 5 kW and a short-term peak output of 10 kW, the servo drive is suitable for high-precision applications, e.g. automated guided vehicles or packaging industries – as a switch cabinet version with protection class IP20 or decentralized version with protection class IP65.
Whitepaper: Recommendations for the deployment of third-party servo drives with EtherNet/IP CIP SyncTM
Machine manufacturers from different industrial segments have high standards for dynamic and precise motion control applications in real-time. By integrating CIP SyncTM in third-party servo drives, it is possible to meet these requirements. Read our whitepaper to learn more about the possibilities and advantages.
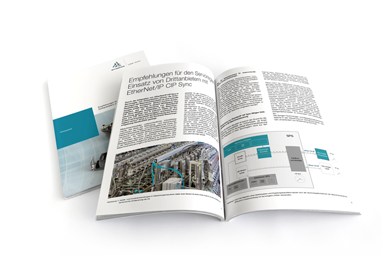
Excellent solution for complex motion tasks
Connectivity
- Multi-Ethernet version
- Many real-time capable fieldbus interfaces
- Various encoder interfaces
Intelligence
- Automatic parameterization thanks to electronic name plate
- Integrated PLC functionality
Safety and robustness
- Integrated safety function STO (SIL3 / PL e)
- Optional safety board (SIM2100): SBC (SIL3 / PL e), SP for EnDat FS (SIL2 / PL d) and safety encoder emulation (SIL2 / PL d)
- 12 to 60 VDC wide range input
- Protection class up to IP65
- Safe communication: PROFIsafe, CIP Safety
Flexibility
- Multi-Ethernet version
- Different performance classes
- Flexible programming of motion tasks
- Protection class IP20 and IP65
- Any mounting position
Easy installation and commissioning
- Compact design
- Connection elements arranged in the front allow simple pin assignment
- Stackability
Dynamics and precision
- Real-time capable and isochronous Ethernet communication
- High current resolution of 14 bits for high-precision torque control
- Switching frequency of 16 kHz
Product highlights
The cyber® simco® drive 2 range includes servo drives for sine-commutated servo motors in the voltage range from 12 to 60 VDC and a maximum power up to 10 kW. The servo drives are available as control cabinet variant or in a decentralized design with protection rating IP65. In combination with the intuitive MotionGUI 2 software, simple parameterization, commissioning and optimization of the system as well as flexible programming of applications is possible.
Space-saving installation thanks to stackability and user-friendly pin assignment
Extremely compact: up to 30% installation space saving
Numerous fieldbus interfaces and decentral intelligence
Simple installation in the machine without enclosure thanks to protection class IP65
Safe shutdown of the system in case of emergency thanks to integrated STO (Safe Torque Off) safety function to SIL3 without loss of productivity
Electronic type plate enables automatic and safe parametrization of the motor
High precision and dynamic torque control to achieve higher machine output
Increased safety functionality thanks to optional safety card (SIM2100): SBC (SIL3 / PL e), SP for EnDat FS (SIL2 / PL d) and safe encoder-emulation (SIL2 / PL d)
Small servo drive system
High-dynamic servo motors in the sizes 17 - 40 mm (optionally with gearbox and ball screw drive)
Numerous fieldbus interfaces and decentral intelligence
Safe shutdown of the system in case of emergency thanks to integrated STO (Safe Torque Off) safety function according to SIL3 without loss of productivity
Space-saving installation thanks to stackability and user-friendly pin assignment
Electronic name plate enables automatic and safe parametrization of the motor
Simple installation in the machine without an additional enclosure thanks to protection class IP65
The cyber® simco® drive 2 servo drive, the cyber® dynamic line motor series and the cyber® dynamic system are a complete match in every respect.
You can choose between numerous different fieldbus interfaces for easy connection to your higher-level controller.
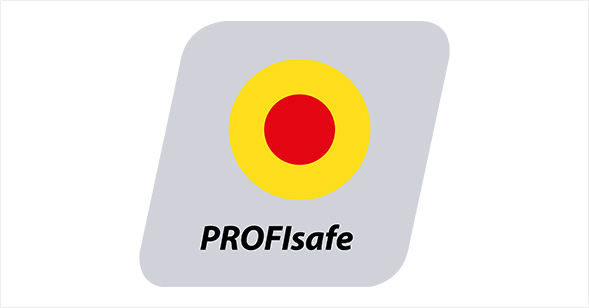
Safe communication via PROFIsafe and CIP Safety
Safe communication interfaces enable fast and safe transmission of safety-relevant data without the need for additional wiring. Certified interfaces according to IEC 61508 up to SIL3 and PL e (Performance Level e) Category 4 meet the highest safety requirements.
The cyber® simco® drive 2 with an optional safety card features the interface: PROFIsafe and CIP Safety. Take advantage of reduced time and cost investment during commissioning, service and documentation for the safe operation of plants and machinery.
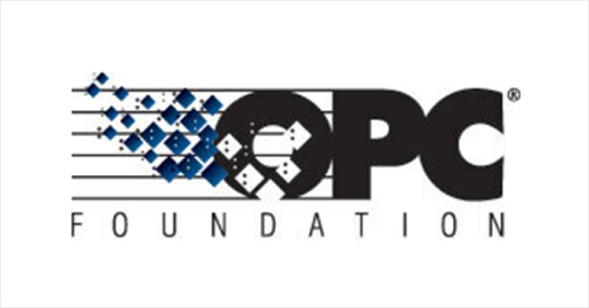
OPC UA - Industry 4.0 interface
Benefit from OPC UA (Open Platform Communications Unified Architecture) for platform- and vendor-independent data exchange. The open interface standard provides you with a reliable, secure and service-oriented architecture for optimal industrial communication from the manufacturing level to the production planning and ERP system or to the cloud.
Our cyber® simco® drive 2 and cyber® dynamic system products have an optional OPC UA server in conjunction with the PROFINET and Ethernet/IP fieldbus variants. This supports the following UPC UA functions: Asset Management, Status Display and Single Axis Motion.